No project is so small that it can’t be made into a learning opportunity. When I found myself in need of some small plugs to seal up a leaky instrument for OSU’s Tanguay Lab I decided to design and print them myself. In order to ensure a good watertight fit I knew they would need to include an O-Ring or some other flexible seal. I’ve never had to design anything with a flexible, compressible o-ring before, so I used the excellent o-ring design guide from EngineersEdge.com to size my components for a 15% compression fit on the o-ring.
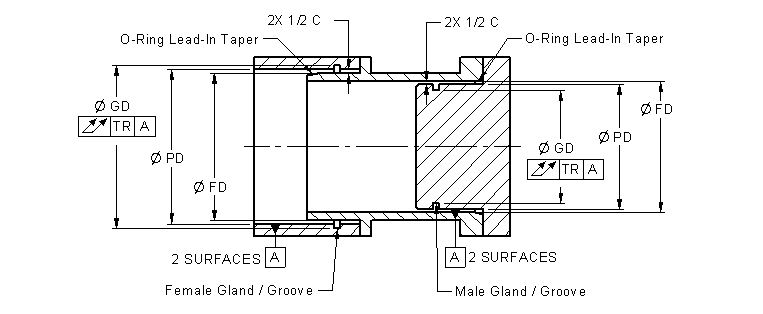
When removing the plugs the user will need some sort of grip. I could have included a basic flange, or nothing at all, but I’ve been wanting to learn how to model nice knurling on my parts for a while now. I followed a YouTube tutorial on knurling using the Coil, Mirror, and Circular Pattern tools and the knurling came out great! I was even able to make it follow the taper of the plugs grip. This is a very simple method, it produces great results, and the process should be similar on other CAD software.
Both of these techniques require a bit of adjustment and tuning to get things just right, so I took a little more time to learn how to use User Parameters in Fusion360. This allows me to create a table of named values and expressions which are referenced by features in my model. For example, if I wanted to change the overall length of the plug I could simply go into the original sketch and modify the corresponding dimension, or I could go to my parameter table and change “TotalLength.” To change the depth of knurling I could just modify that parameter in the Coil feature, or change the “CoilDepth” parameter in the table. For a small part with only a few features such as this one, it might not matter much either way. But I usually work with much larger models including dozens of sketches, extrusions, holes, and other features. I could (and in fact do) quickly get lost in trying to find which sketch describes feature X, or which extrusion sets the height of Y. By giving each of these values a descriptive name in the User Parameter table, I can quickly look up and change the values of X or Y in one place. I really can’t believe I haven’t been using this all along, I can already tell that this one feature is going to really change the way I work going forward!
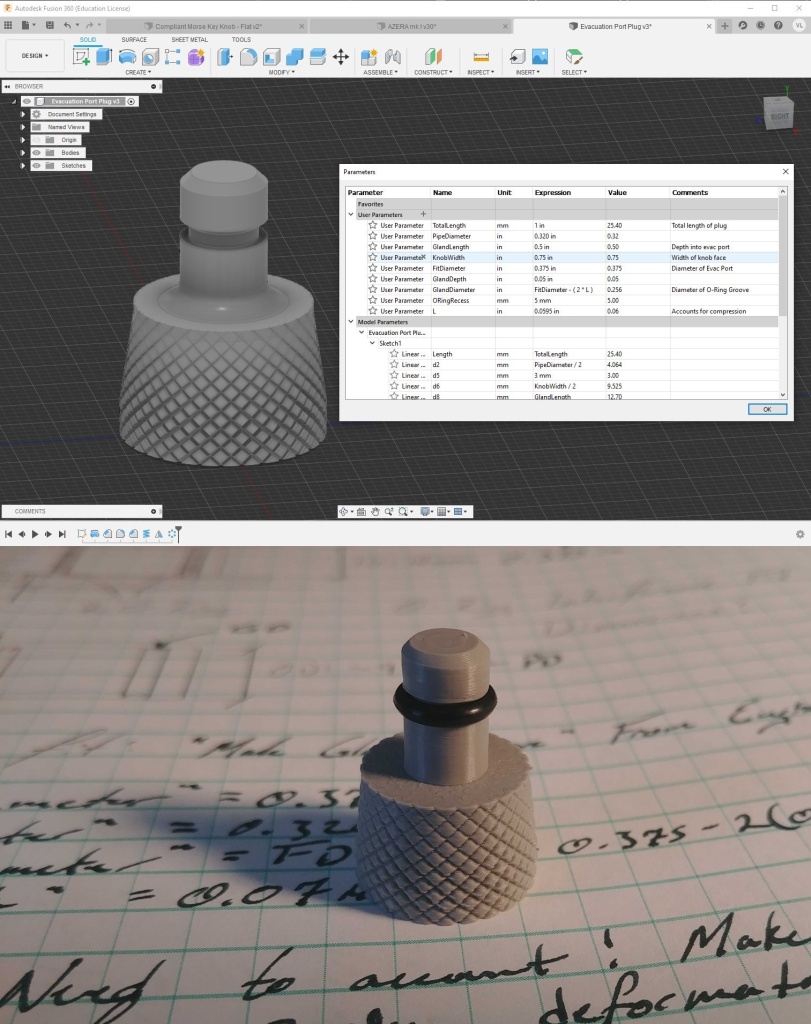
Small projects like this one are a perfect opportunity to experiment with different techniques and learn new things, though it may be easier to keep doing what you’ve always done. I could have made these plugs “good enough” in about 5 minutes, but by taking the time to make them the way I really wanted them to be I learned a few things that will help improve bigger, more important projects in the future. Only by consciously stepping outside of our routines can we expand our abilities and grow. So next time you have some small task to get done, remember that you can realize big improvements from small projects!